マシニングセンターによるブロックの加工① 表面
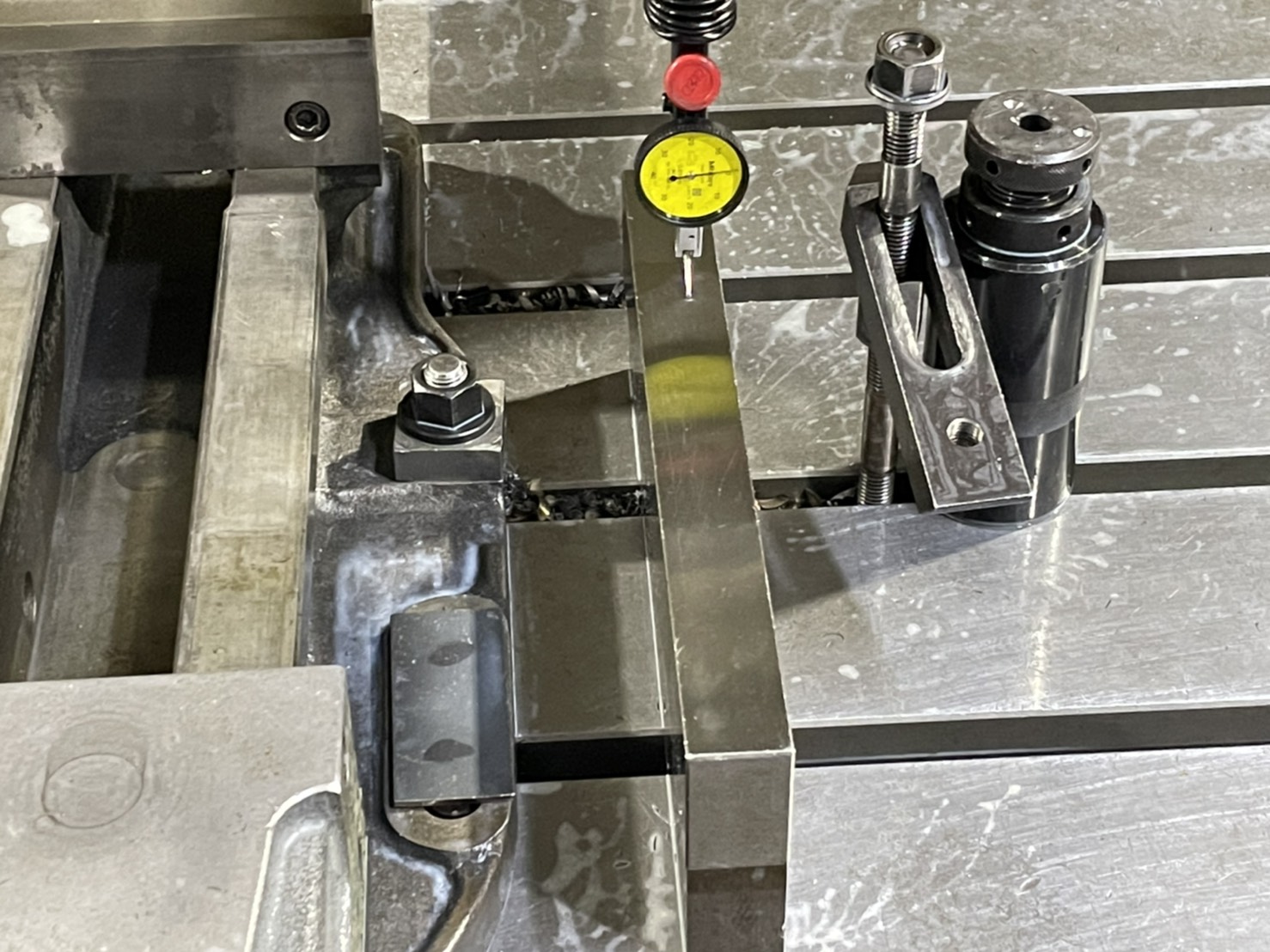
2回に分けてご紹介する「マシニングセンターによるブロック加工」。
今回は前半部分として、表面加工の工程をご紹介します。
まずは、機械加工する前の段取り(準備)です。
段取りとは
- 加工プログラムの作成
- 刃物の選定とツールホルダーへの取り付け(ツーリング)
- 材料を加工テーブルへ取付(固定 クランプ)
主にこの3つとなります。
今回、製作する部品は並行 5/100mm という標準的な加工になります。
ただし、今回使用する材質の SS400 は、ひとくくりにSS400と言っても、単体のくせにバラつきがある粗い材料です。
バラつきを見極める方法としてタップの切粉に特徴があるのですがそれを言葉に表す事ができません。
「勘」です。
先に側面のタップ加工をして見極めました。今回のこの材料は「反りにくい」と判断しました。
反りにくいということは、加工の際に気を使う点が減るという意味で、ありがたいことです。
早速、固定(クランプ)方法を決めます。
バイスで並行をとり、両端の下駄に載せて垂直クランプ2箇所で固定します。
下駄は研磨をして 1/100mmの面(平面)を出しました。
このような感じで固定しました。
続いてプログラムと刃物のツーリングを行い加工開始。
加工工程、どのようなツールを使うかなどをご説明します。
自動芯だしツールです。とても便利です! 自動で材料の位置を割り出してくれます。
難点は設定を間違えてツールをぶつけて壊すと修理費に目が飛び出る事です(笑)
最初に平面の粗挽きを高送りという方法で加工します。
平面の仕上げ加工です。ショルダーミルという刃物を使います。
ショルダーミルは刃先の角が1Rなので、図面指示を守るためにエンドミルでもう一度加工します。
コーナーR0.3のエンドミルです。
大型マシニングはツールの長さがバラついてしまうため、微調整が必要です。
微調整の幅は0.05mm以内です。
続いて穴を開けていきます。
センタードリルです。
最初からドリルで開けると穴がズレてしまうのでその位置を確実にするために使用します。
ドリル加工です。5種類のドリルを使いました。
そして公差(精度)の厳しい穴を加工します。4本のエンドミルを使いました。
寸法チェックをします。
寸法、OKでした!! 次に進みます。
ドリル穴に面取り加工をしました。
次はタップ加工ですが、次工程で裏面から加工することにしました。
並行度 5/100mm を確認して表面の加工は終わりです。
刃物は全部で14本を使いました。
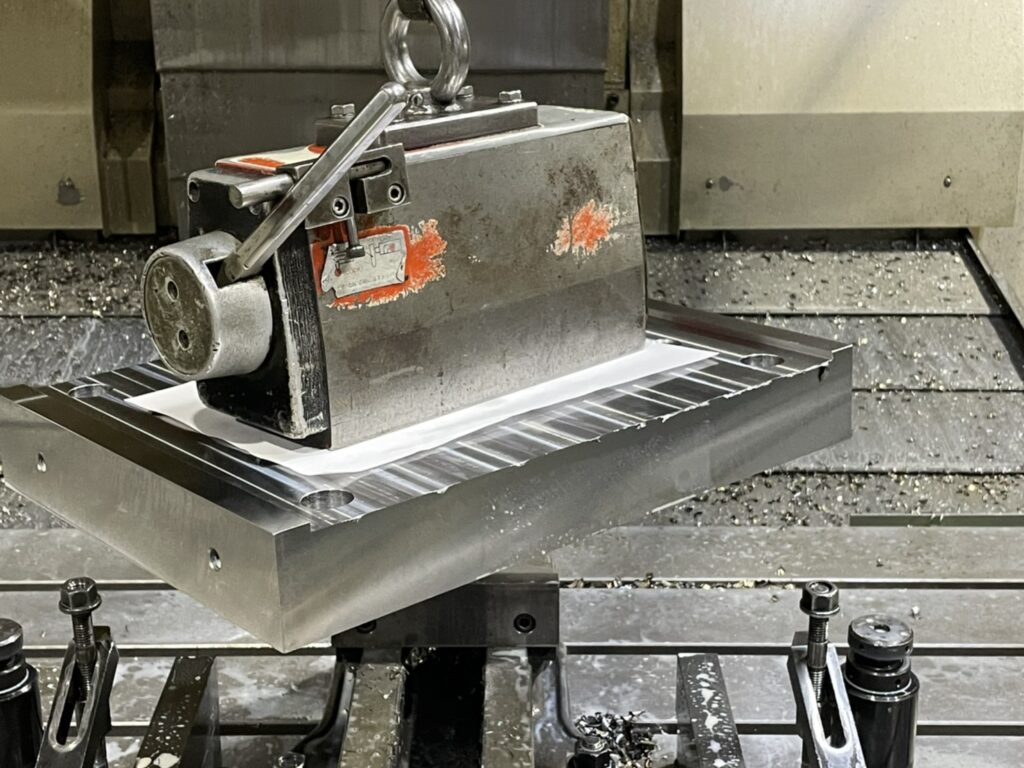
豆知識ですが、マグネットチャックと製品の間に紙を挟むだけで傷が付きにくくなります。
以上、マシニングセンターによる加工事例の報告でした。
裏面の加工は「マシニングセンターによるブロックの加工② 裏面」をご覧ください。
茂呂製作所には 縦1000mm 横2000mm 高さ1000mmの加工ができるマシニングセンターが2台あります。
同じ機械が2台あるので、試作と量産が両方可能です。