アルミ合金を加工して「富士山」製作!
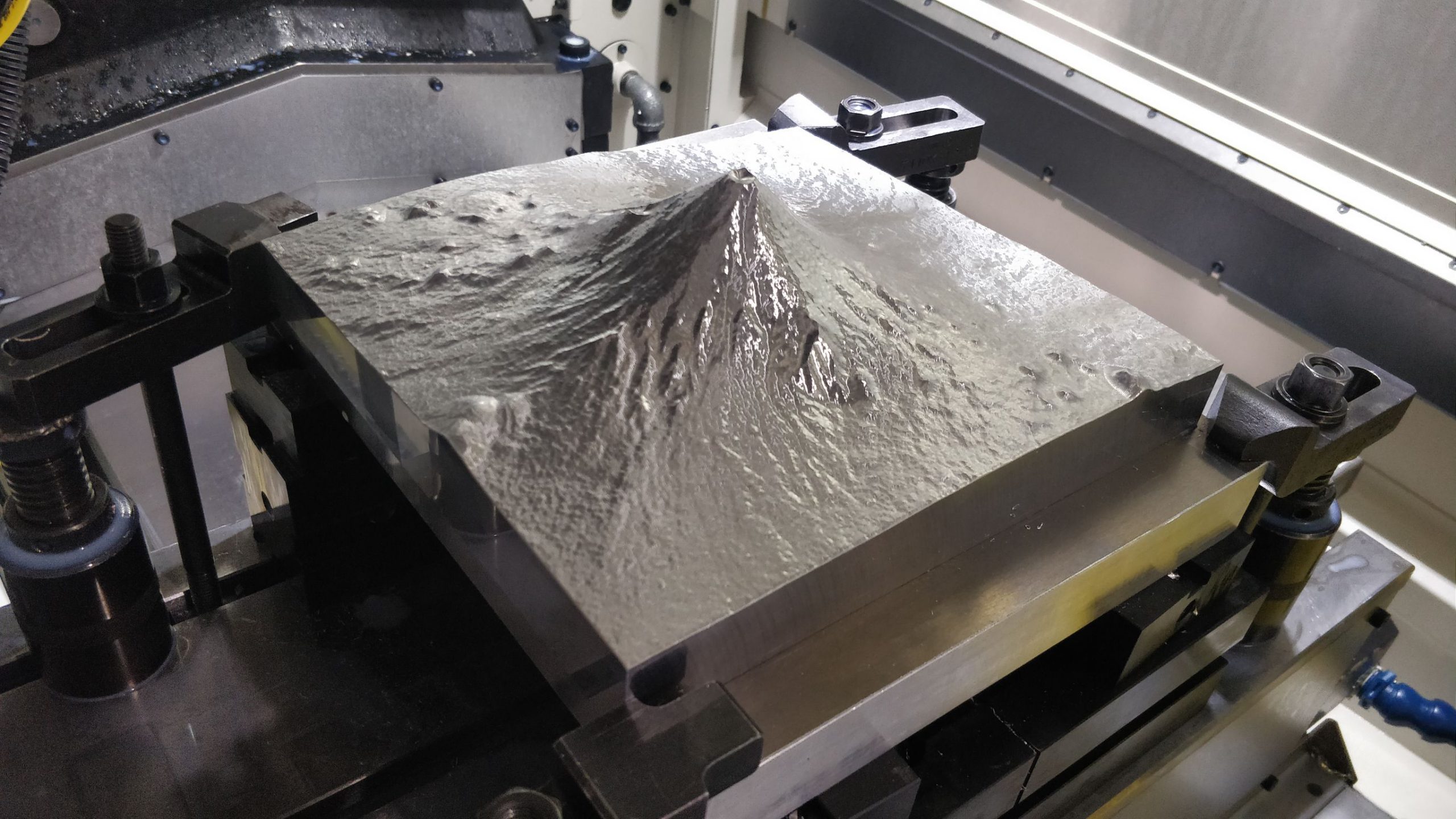
弊社にはタイ人3名、ベトナム人5名、インドネシア人3名、計11名の外国人実習生や技術者がいます。
彼らには、技術を学ぶだけでなく、この土地への愛着を持ち、将来母国に帰っても相互の理解と友好の懸け橋となってほしい、そんな思いを抱いています。
そこで今回は、インドネシアからの技術者ディロンくんに、技術教育も兼ね、普段製作している加工品とは打って変わって、日本のシンボルであり山梨のシンボルでもある「富士山」をアルミ合金で製作してもらいました。
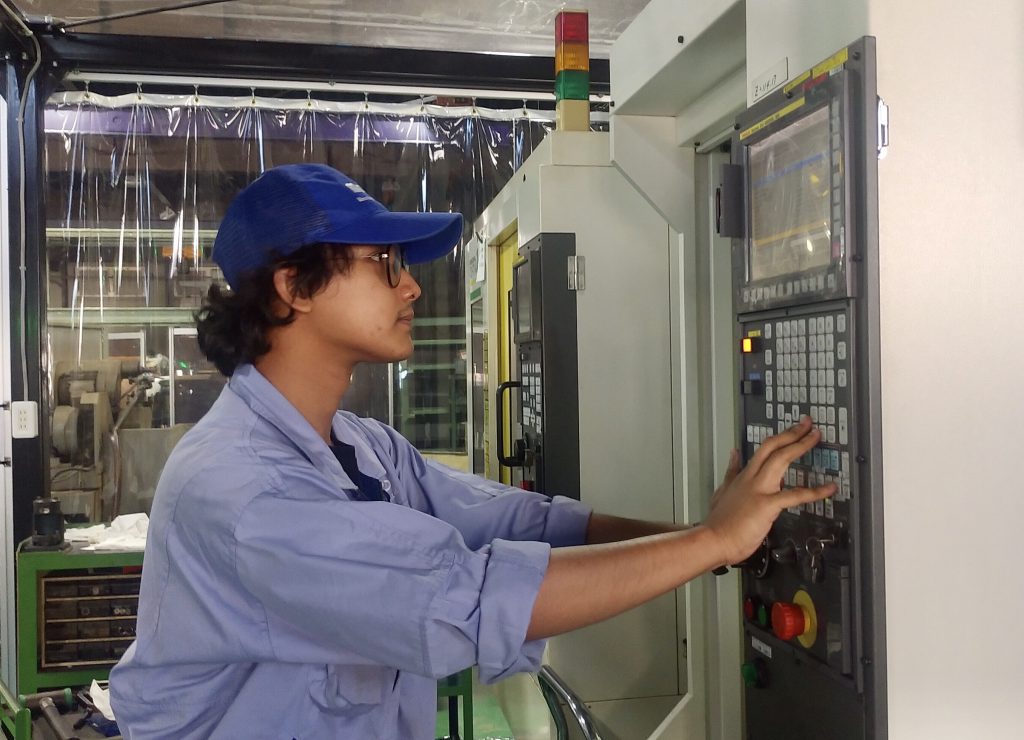
まずは形をプログラミング
まずは、富士山の形をプログラミングします。
彼の実家は機械加工の会社を営んでおり、彼はそこで治具部品の設計を行っていました。
治具設計以外にも、機械加工やプログラミングも手伝っていたようです。
そのため、プログラミングはお手の元です。
実はディロンくん、日本に来る前に富士山の形をプログラミングしたデータをすでに用意していました。
いつか作ってみたいという想いを抱いていたようで、ディロンくんの想いと、茂呂製作所の想いと、新型コロナウィルスの影響でたまたま空き時間ができたことと、様々な要因が重なって今回の製作に至りました。
対象物を固定する治具の製作
加工に入る前に、対象物を固定するための治具を製作します。
治具を使用せずに加工すると、対象物がドリルの抵抗に耐えきれず、動いてしまうリスクがあります。
今回は、中心を基準に5箇所穴を開け、対象物の裏側にネジ穴を切り、治具と対象物をボルトでつなぎました。
治具の四隅をクランプで固定すれば、加工前段階終了です。
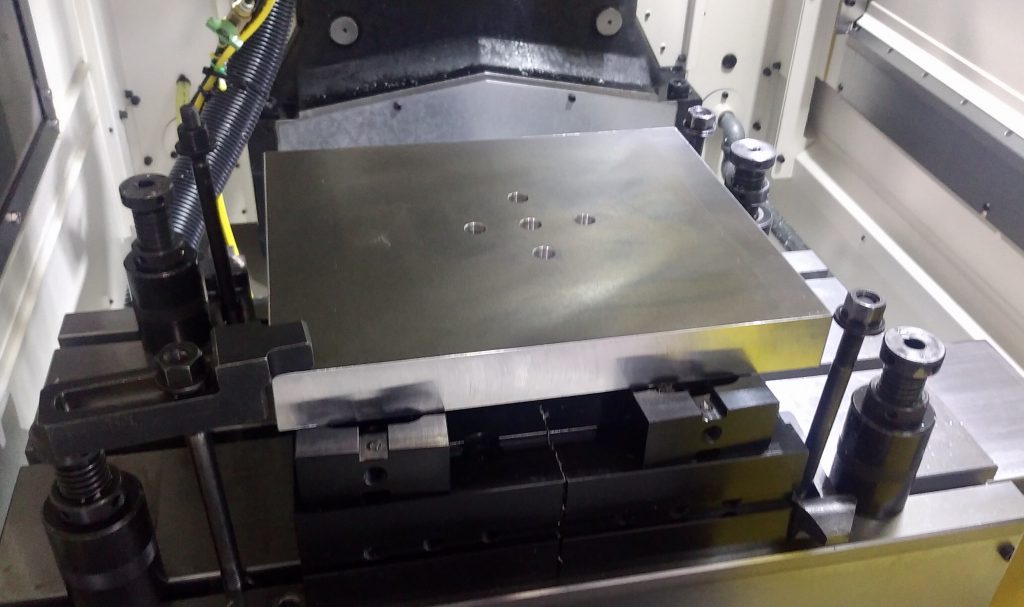
いよいよ加工の工程
いよいよ、実際の加工に入ります。
アルミの切削加工は、材料が柔らかいため、下記のような欠点があります。
- 切り粉で傷がつきやすい
- 摩擦熱で歪みやすい
そのため、クーラントを用いて刃先を冷却したり、高速で切削するなどの対策が必要です。
今回の対象物のサイズは250×230×80。
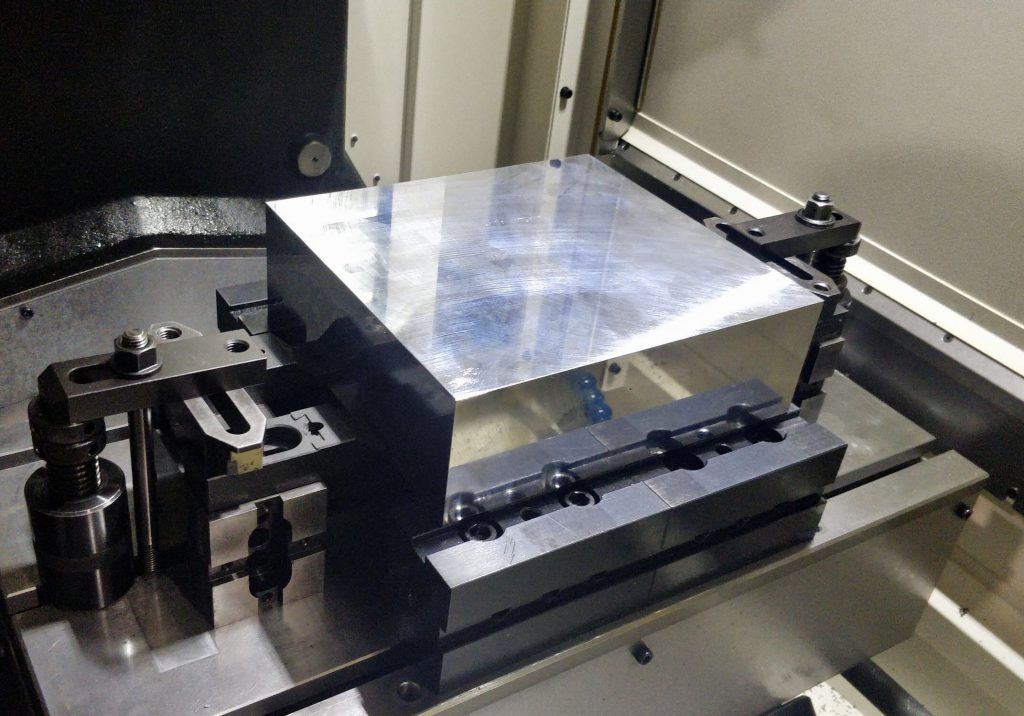
使用するエンドミルは、左からΦ16・10・4。
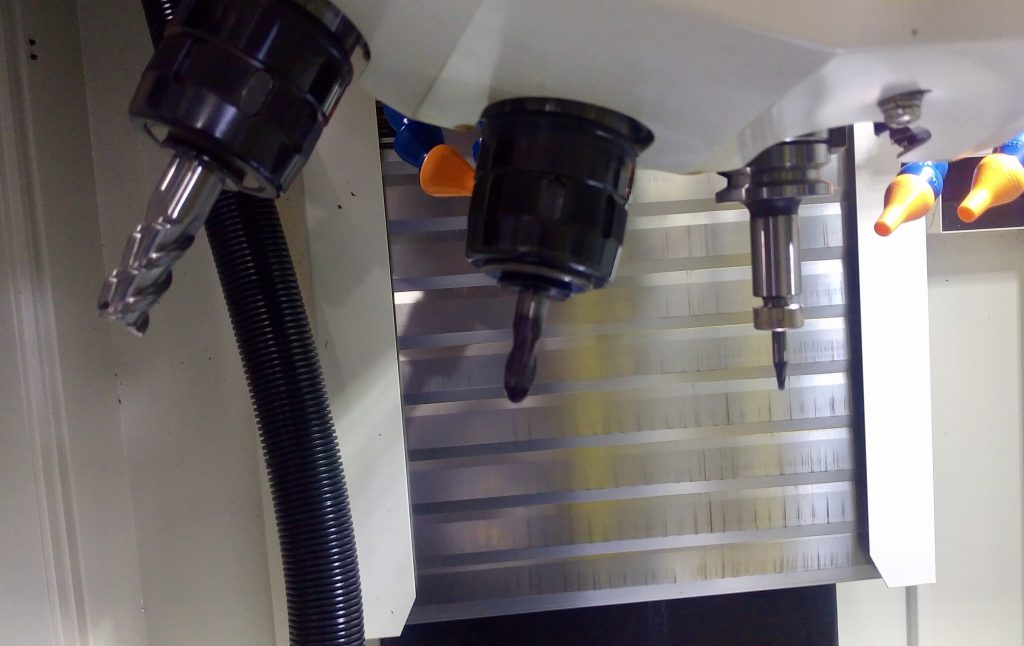
まずは、Φ16エンドミルで荒出しです。
ここである程度の形にしていきます。
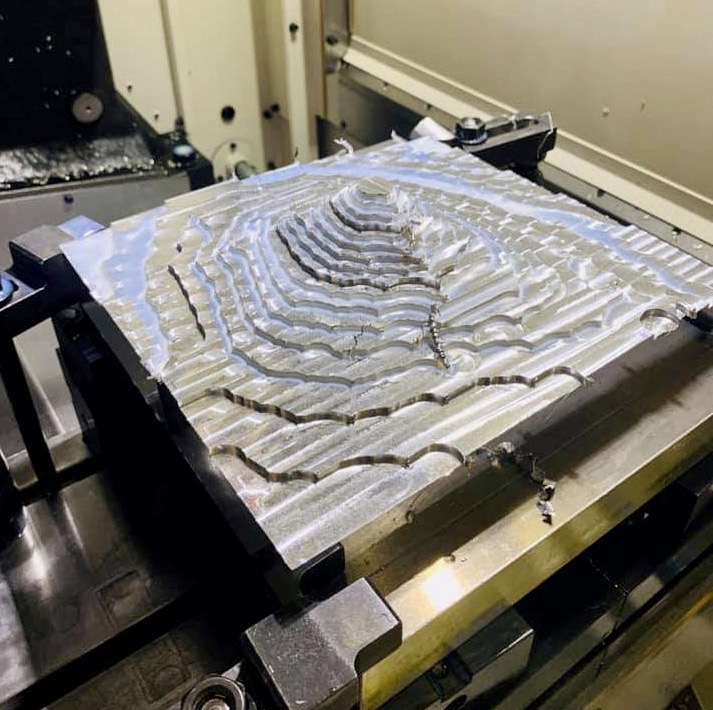
Φ10ボールエンドミルでさらに富士山の形を再現していきます。
この時点でかなり形になってきていますね。
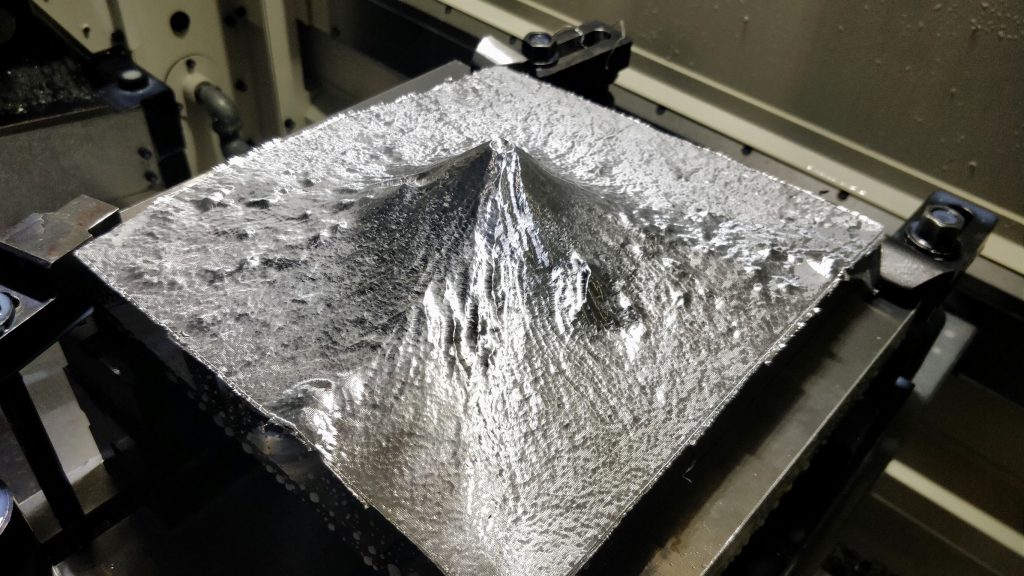
最後に、Φ4ボールエンドミルで仕上げ作業に入ります。
表面をなだらかにし、完成です。
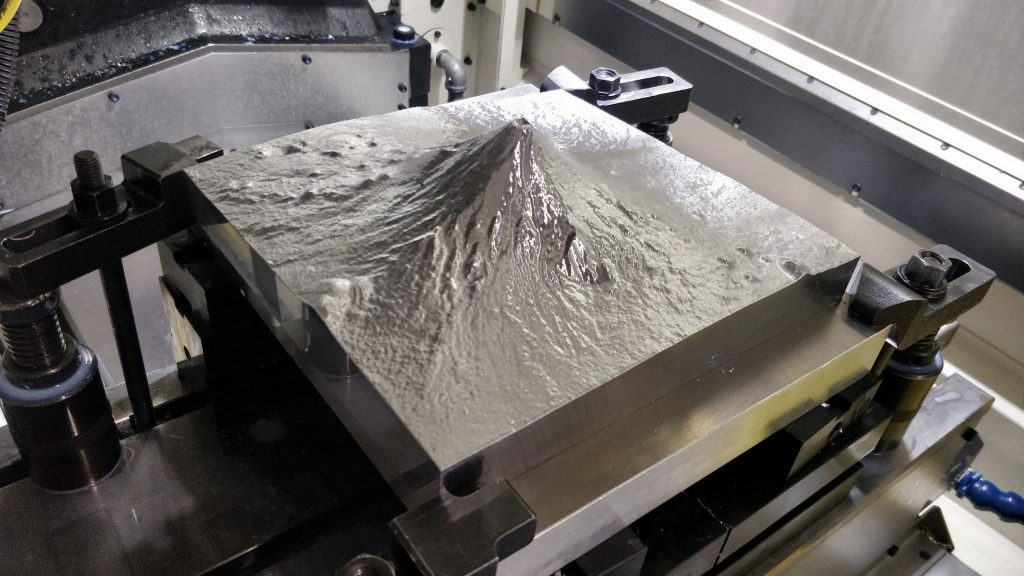
作業工程まとめ
作業工程と日数をまとめます。
①クランプジグ作成
②富士山プログラミング
③プログラムのチェックや補正【一週間半(①〜③)】
④加工 Φ16エンドミル【5.5h】
⑤加工 Φ10ボールエンドミル【5h】
⑥加工 Φ4ボールエンドミル【3h】
苦労した点
今回苦労したのは3点、「固定用治具の製作」と「作成したプログラムの機械へのデータ転送」、「プログラムデータの補正」です。
その① 固定用治具の製作
当初は、クランプのみでワークを挟み加工したのですが、固定が甘く、刃物が当たったときにワークが動いてしまいました。
そのため、治具を製作し固定することにしました。
固定用治具の形には正解がなく、その時々に最適な形を製作しなければなりません。
実は、完成品の裏側に失敗の跡が残っています。
その② データ転送
データ転送時には、「バッファオーバーフロー」というエラーが出ました。
これはパソコンと機械を直接繋いだ時に出るもので、プログラムの容量が大きいため機械のバッファから溢れるという現象です。
実際に機械を動かしていくと途中で止まってしまいます。
そこで、まずPCカードを試してみました。
これでDNC運転(Direct Numerical Control(直接数値制御の頭文字)に切り替わり、駆動部に直接データ送信が可能になります。
ただ、これも通信速度の規格なのかうまくいきませんでした。
次に、コンパクトフラッシュを試してみます。
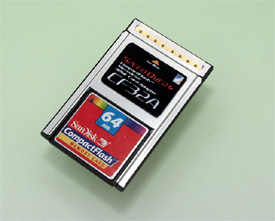
今度はうまく転送ができました。
ディロンくんはコンパクトフラッシュを知らなかったようで、ベテラン技術者の長年の知恵を借りて、問題解決です。
その③ プログラムデータの補正
プログラムデータの作成と対象物の固定が完了すれば、あとはボタン一つでマシニングセンタが加工してくれるのですが、各工程でプログラム通りに動くか確認しながら進めていきます。
プログラム通りに動かない箇所ではアラートが出るので、そんな時には手打ちで補正を行います。
ここは技術部課長が最後までサポートします。
加工を終えて
ディロンくんに今回の感想を聞いてみました。
苦労した点は、先ほど述べたように、正解がない分固定用治具をどのような形にするか悩んだようです。
楽しかった点は、「強いて言うなら、Φ4での加工途中で富士山がだんだんと仕上がっていくところですが、全部楽しかったです!」と話してくれました。
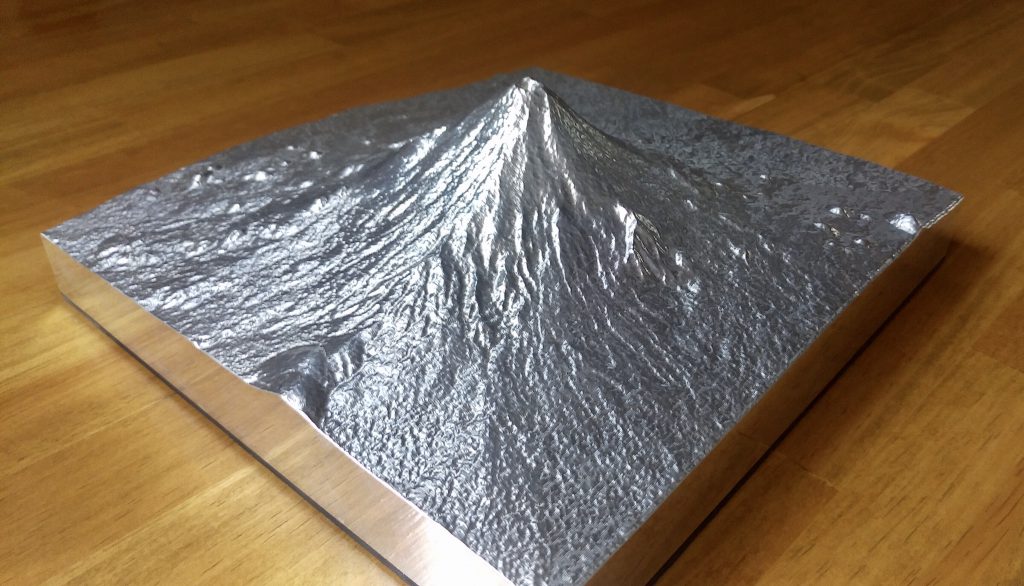
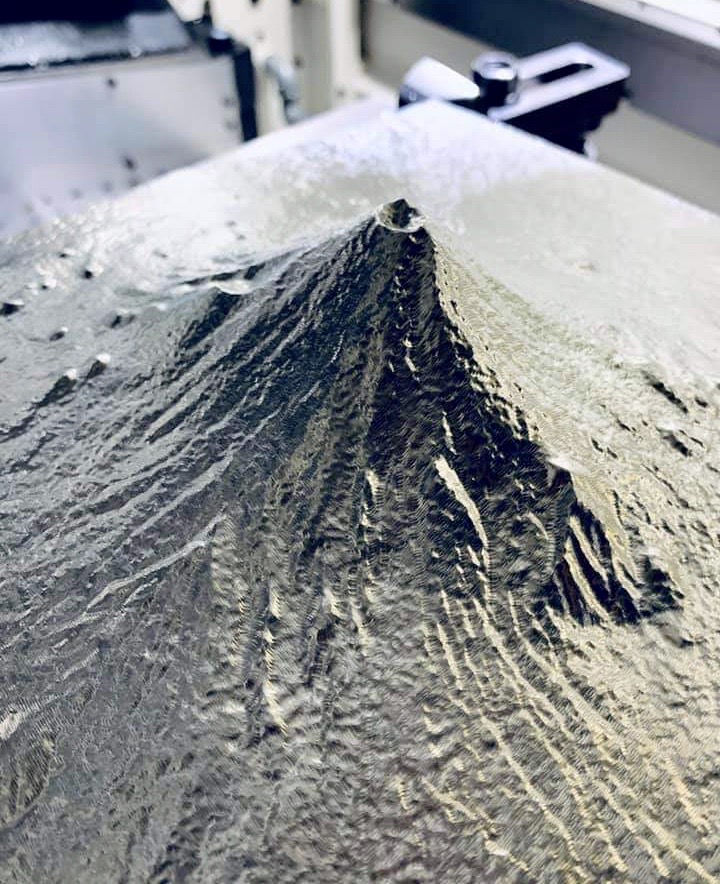
最後に、執筆者から一言!
外国人実習生や技術者に対して、ただ彼らに技術を覚えてもらうだけでなく、時には業務から離れて、「モノづくり」を心から楽しんでもらう時間も大切です。
遊びと思われるかもしれませんが、一緒に取り組んだ上司も含め、「遊びも本気で」向き合っているからこそ、普段から良いモノづくりができるのだと思います。
今回、「全部楽しかった」と言ってくれたディロンくんも、「遊びも本気で」取り組んだ証拠ですね。